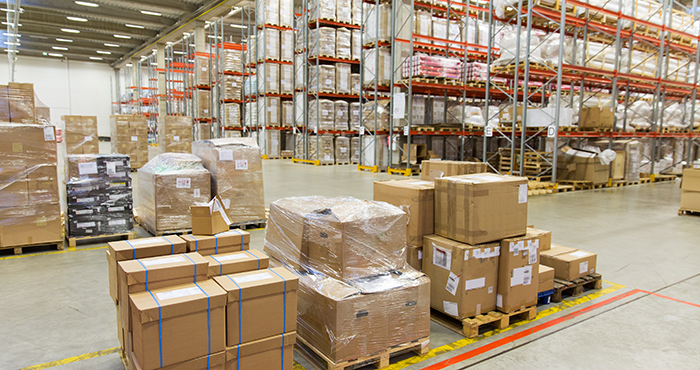
"Just In Time" And Today's Global Uncertainty
It was only a decade ago when a firm protected itself against uncertainty by maintaining a reserve inventory both with their production and stocking points (warehouse) for "just in case". This philosophy of inventory management led to unnecessarily high levels of inventory, and was only possible if you had adequate space and the capital to support it.
In contrast, many Canadian organizations use the "just in time" concept. This is an inventory supply system that operates with very low inventories requiring less resources, but requires fast, on time delivery. When supplies are needed, they arrive from suppliers just in time, which means less product on a more frequent basis.
As an example, Toyota, like many automobile companies, engages in a just in time inventory system that keeps inventories of automobile components to a minimum because the company only orders them from suppliers to arrive just in time to be used. But even the best just in time systems can face unforeseen situations.
Toyota experienced a just in time inventory system challenge when, early one morning, a factory that supplied brake fluid proportioning valves to Toyota's 20 automobile plants in Japan, became engulfed in flames. Scheduled to produce 14,000 cars per day with a just in time inventory system (a window of about four hours), Toyota faced a crippling dilemma that could have potentially shut production down for weeks.
Unpredictable global tragic events increase the fragility of global supply chains. Supply chains will likely need to be made more resilient, which could occur in one of two ways:
- Identify more than one source of supply for key inventory that may come from locations that are geographically separated; or
- Re-think the use of "just in case"
There will always be periods when the supply chain is disrupted, but do those periods justify keeping extra inventory? Although you may lose when the disaster occurs, organizations are in business for the long term and "just in case" is something of the past. We should learn from the waste setbacks and continue to find ways to improve our supply chain systems.
Unforeseen events, such as the disaster in Japan, are bound to put pressure on our business processes. However, "just in time" helps reduce waste and it would be taking backward steps if we reverted back to the "just in case" concept.
How To Kick Trade Anxiety Out Of Your Business In 4 Steps
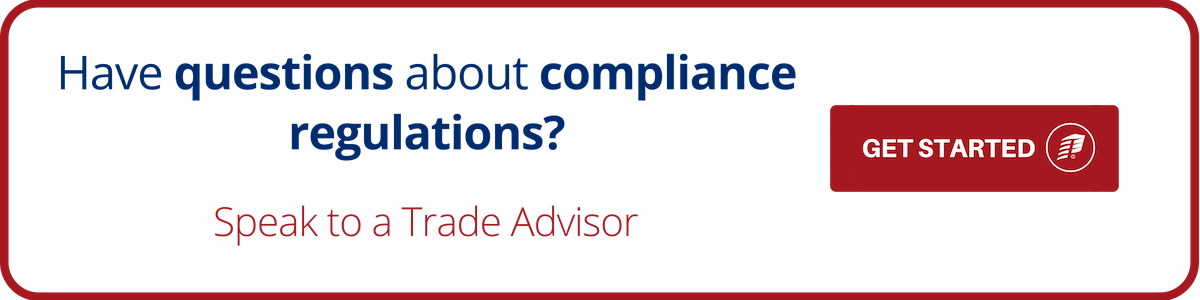